Carbon Neutrality Roadmap
POSCO is advancing towards a low-carbon production system based on the ‘2050 Carbon Neutrality Roadmap’, which includes a mid- to long-term comprehensive carbon reduction strategy encompassing technology development, facility investment, raw material procurement, and energy procurement.
Carbon Neutrality Roadmap
In the mid- to short-term, we plan to reduce carbon emissions by expanding the use of low-carbon fuel and raw materials, operating at a low HMR (Hot Metal Ratio), and introducing EAFS using the current facilities through low-carbon bridge technology. In the long-term, we aim to achieve carbon neutrality by gradually implementing POSCO’s hydrogen reduction ironmaking technology, ‘HyREX (Hydrogen Reduction).’
1)Average total emissions from POSCO’s domestic operations between 2017 and 2019
2)Added a 2035 mid-term goal (▲30%) under the net zero roadmap
Blast Furnace-Based Low-Carbon Bridge Technology : Use of Low-Carbon Fuel and Raw Materials
Pellets are raw materials processed into spherical shapes of a certain size after crushing and screening iron ore. Simply switching the blast furnace raw material from sintered ore to pellets can reduce the fossil fuel used in sintered ore production. HBI (Hot Briquetted Iron) is a raw material that has undergone a reduction process to remove oxygen from iron ore. When HBI is fed into the blast furnace, it reduces the amount of coking coal required for reduction. Generally, using 100kg of HBI per ton of molten iron production reduces CO2 emissions by 100kg compared to sintered ore. POSCO is planning an HBI production project in iron ore-rich Australia to ensure a stable supply of HBI.
-
Key Bridge Technologies Based on Blast Furnace/Converter
-
Scrap UsagePurchased ScrapSelf-Generated Scrap
* Future scrap usage may vary according to the company's carbon neutrality strrategy
Converter based Bridge Technology: Melted Scrap Charging Method, Oxygen Top & Bottom Blown(OTBB) Converter
The converter,BOF(Basic Oxygen Furnace) is a large cauldron-shaped facility that holds molten iron produced in a blast furnace. By blowing oxygen into the molten iron, impurities are removed, and refined steel with desired components is produced. Assuming the total carbon emissions for producing one ton of molten steel is 100%, approximately 80% is generated during the production of molten iron. Therefore, converter-based bridge technology aims to reduce the amount of molten iron used in the converter and increase the amount of scrap.
There are mainly two approaches to reduce the amount of molten iron in the converter.
There are mainly two approaches to reduce the amount of molten iron in the converter.
Melted Scrap Charging Method Technology
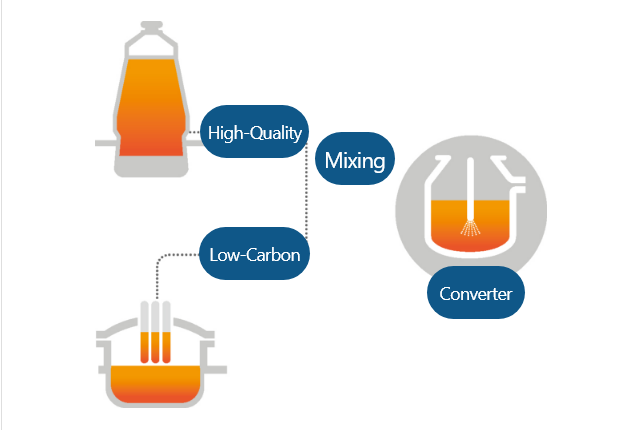
The first technology is ‘Melted Scrap Charging Method,’ which increases the scrap ratio used in the converter by pre-melting the scrap.
EAF can recycle steel scrap to produce steel, reducing carbon emissions to one-fourth of the levels produced by blast furnaces. However, due to the limitations in producing high-grade products depending on the components and impurities of the steel scrap, high-grade steel such as automotive steel sheets and shipbuilding plates are currently mostly produced by refining blast furnace molten iron in converters.
POSCO plans to operate a large electric arc furnace with an annual production capacity of 2.5 million tons starting in 2026. This technology, which combines blast furnace molten iron with EAF steel, aims to simultaneously reduce carbon emissions and produce high-grade steel. Producing 2.5 million tons of steel in the EAF is expected to reduce carbon emissions by up to 3.5 million tons annually compared to the company’s blast furnace method.
EAF can recycle steel scrap to produce steel, reducing carbon emissions to one-fourth of the levels produced by blast furnaces. However, due to the limitations in producing high-grade products depending on the components and impurities of the steel scrap, high-grade steel such as automotive steel sheets and shipbuilding plates are currently mostly produced by refining blast furnace molten iron in converters.
POSCO plans to operate a large electric arc furnace with an annual production capacity of 2.5 million tons starting in 2026. This technology, which combines blast furnace molten iron with EAF steel, aims to simultaneously reduce carbon emissions and produce high-grade steel. Producing 2.5 million tons of steel in the EAF is expected to reduce carbon emissions by up to 3.5 million tons annually compared to the company’s blast furnace method.
Oxygen Top & Bottom Blown(OTBB) Converter Technology
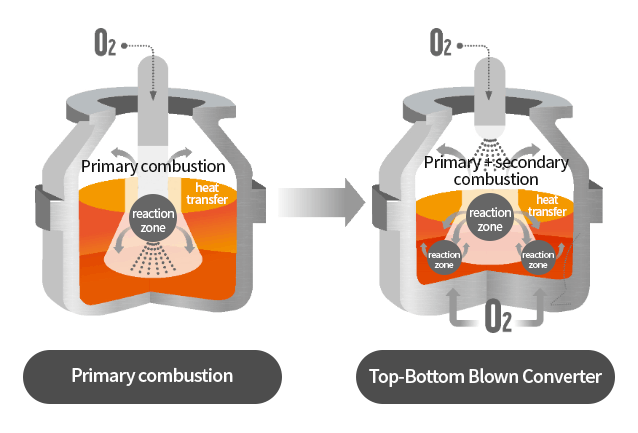
The second technology is the ‘OTBB Converter Technology,’ which introduces additional heat sources by blowing oxygen from both the top and bottom of the converter to increase the use of steel scrap. Since the converter does not receive external heat, it relies on the heat generated by the oxidation reactions of impurities in the molten iron.
Increasing the amount of steel scrap lowers the temperature of the molten iron.
However, OTBB Converter technology supplies additional heat by injecting oxygen from the bottom, as well as the top, maximizing secondary combustion and heat transfer efficiency within the converter. One of the main advantages of steel is the ease of scrap recovery and its repetitive recyclability. Technologies that enable the extensive use of steel scrap instead of molten iron, like Melted Scrap Charging Method or OTBB Converter technology, are collectively referred to as ‘Low HMR (Hot Metal Ratio) Operation Technology.’
We expect that using molten iron from FINEX process may allow the hot metal ratio (HMR) in the converter to be below 70%. Currently, development and investment in OTBB Converter technology are underway, with plans to complete a 300-ton OTBB converter at Pohang Steelworks by 2026.
Increasing the amount of steel scrap lowers the temperature of the molten iron.
However, OTBB Converter technology supplies additional heat by injecting oxygen from the bottom, as well as the top, maximizing secondary combustion and heat transfer efficiency within the converter. One of the main advantages of steel is the ease of scrap recovery and its repetitive recyclability. Technologies that enable the extensive use of steel scrap instead of molten iron, like Melted Scrap Charging Method or OTBB Converter technology, are collectively referred to as ‘Low HMR (Hot Metal Ratio) Operation Technology.’
We expect that using molten iron from FINEX process may allow the hot metal ratio (HMR) in the converter to be below 70%. Currently, development and investment in OTBB Converter technology are underway, with plans to complete a 300-ton OTBB converter at Pohang Steelworks by 2026.
FINEX-Based Bridge Technology : Carbon Capture and Utilization (CCU)
Since 2021, POSCO, in collaboration with the Research Institute of Industrial Science & Technology (RIST), has been conducting a public-private joint national R&D project to demonstrate carbon dioxide capture and conversion technology. This technology separates and captures high-purity CO₂ from high-temperature gases generated in blast furnaces, converters, and FINEX melting furnaces, then injects the CO₂ into the coke oven to be used as a heat source for byproduct gas power generation.
In January 2024, demonstration results at Pohang Steelworks revealed that injecting CO₂ at a medium purity level of 65-70% into the coke oven is economically feasible, as it does not require additional energy for further purification. Additionally, the calorific value of the coke oven gas (COG) increased by approximately 7%. Expanding this application to Pohang and Gwangyang Steelworks is expected to reduce CO₂ emissions by 320,000 tons annually. Furthermore, the commercialization of liquid carbon dioxide production using medium purity CO₂ byproduct gas is underway. This will enable the economic production of liquid carbon dioxide with a purity level of 99.99%, potentially expanding the industrial gas product portfolio and reducing CO₂ emissions by 170,000 tons annually (assuming the production of 200,000 tons of liquid carbon dioxide per unit).
In January 2024, demonstration results at Pohang Steelworks revealed that injecting CO₂ at a medium purity level of 65-70% into the coke oven is economically feasible, as it does not require additional energy for further purification. Additionally, the calorific value of the coke oven gas (COG) increased by approximately 7%. Expanding this application to Pohang and Gwangyang Steelworks is expected to reduce CO₂ emissions by 320,000 tons annually. Furthermore, the commercialization of liquid carbon dioxide production using medium purity CO₂ byproduct gas is underway. This will enable the economic production of liquid carbon dioxide with a purity level of 99.99%, potentially expanding the industrial gas product portfolio and reducing CO₂ emissions by 170,000 tons annually (assuming the production of 200,000 tons of liquid carbon dioxide per unit).
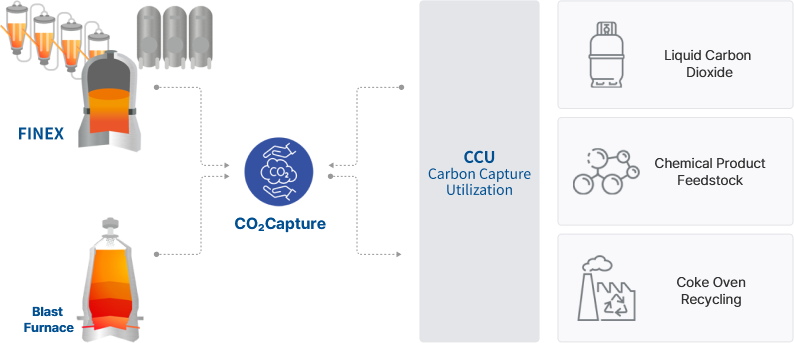
Key CCU Patent List (POSCO, RIST)
Division | Main Content |
---|---|
1019408380000 | Method for heating injected gas in coke oven |
1015337740000 | Gas injection device for coke oven |
1015608860000 | Coke oven and its use in injecting reaction gas |
1018193400000 | Gas dispersion device for coke furnace |
1018791060000 | Method for heating injected gas in coke oven and coke oven |
1020430120000 | Device and method for producing injected gas for coke oven |
POSCO’s Hydrogen Reduction Ironmaking (HyREX)
Hydrogen reduction ironmaking is a technology that replaces metallurgical coal used as a reducing agent and heat source in the ironmaking process with hydrogen, drastically reducing GHG emissions. Recognized for its strategic importance to national security and its overall impact on the national economy, hydrogen reduction ironmaking technology was designated as a National Strategic Technology in January 2024.
Features of HyREX
POSCO’s proprietary hydrogen reduction ironmaking technology, HyREX, is based on the fluidized bed reduction furnace technology of the already commercialized FINEX process. This differs significantly in terms of raw materials and equipment technology from the shaft furnace method used by overseas steel companies.
From a raw material perspective, the shaft furnace uses pellets made by processing iron ore into uniform spherical shapes, but HyREX can use fine ore directly, making raw material procurement easier and production costs more economical. From an equipment technology perspective, HyREX’s fluidized bed reduction furnace technology offers superior temperature control compared to the shaft furnace. Most importantly, POSCO’s FINEX process, based on the fluidized bed reduction furnace, already incorporates hydrogen injection and direct reduced iron (DRI) manufacturing technology, which are key components of hydrogen reduction ironmaking, making it the most advantageous technology for implementing hydrogen reduction ironmaking.
From a raw material perspective, the shaft furnace uses pellets made by processing iron ore into uniform spherical shapes, but HyREX can use fine ore directly, making raw material procurement easier and production costs more economical. From an equipment technology perspective, HyREX’s fluidized bed reduction furnace technology offers superior temperature control compared to the shaft furnace. Most importantly, POSCO’s FINEX process, based on the fluidized bed reduction furnace, already incorporates hydrogen injection and direct reduced iron (DRI) manufacturing technology, which are key components of hydrogen reduction ironmaking, making it the most advantageous technology for implementing hydrogen reduction ironmaking.
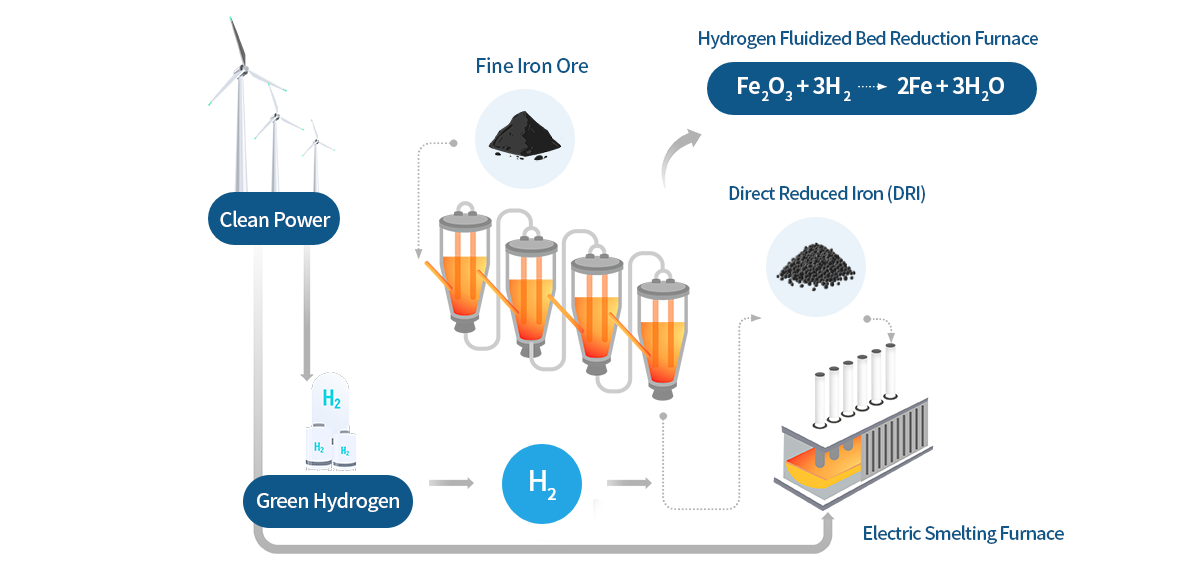
HyREX Implementation Plan
POSCO embarked on obtaining the necessary permits and approvals for the 1.35 million square meter construction site of its hydrogen reduction ironmaking plant at Pohang Steelworks in 2021. In July 2022, POSCO entered into an engineering partnership agreement with Primetals, leveraging their expertise in FINEX facility design, to collaboratively work on the main facilities of the HyREX demonstration plant. In 2023, POSCO introduced a hydrogen fluidized bed reduction experimental furnace with a capacity of 50kg per batch at RIST to validate the hydrogen fluidized bed reduction technology. By April 2024, POSCO had completed and successfully tested a 1-ton per hour electric smelting furnace (ESF) pilot facility at Pohang Steelworks. This achievement laid a solid foundation for the development of core technologies essential to the electric smelting furnace and the commercialization of HyREX technology.
POSCO plans to develop and commercialize the core technology of the hydrogen reduction ironmaking process, the hydrogen fluidized bed reduction furnace, by 2030. By 2050, POSCO aims to gradually transition existing blast furnace facilities to HyREX facilities, achieving carbon neutrality. POSCO is also actively involved in forming technology development partnerships to drive the implementation of carbon neutrality within the global steel industry.
In partnership with the worldsteel and Swedish steel company SSAB, POSCO spearheaded the international Hydrogen Iron and Steel Making Forum (HyIS) from 2021 to 2022. From 2023 onwards, the HyIS forum will expand and evolve into the ‘Breakthrough Technology Conference,’ overseen by the worldsteel. POSCO will continue to accelerate low-carbon technology development in the steel industry through collaboration with global steelmakers, fostering cooperation over competition.
POSCO plans to develop and commercialize the core technology of the hydrogen reduction ironmaking process, the hydrogen fluidized bed reduction furnace, by 2030. By 2050, POSCO aims to gradually transition existing blast furnace facilities to HyREX facilities, achieving carbon neutrality. POSCO is also actively involved in forming technology development partnerships to drive the implementation of carbon neutrality within the global steel industry.
In partnership with the worldsteel and Swedish steel company SSAB, POSCO spearheaded the international Hydrogen Iron and Steel Making Forum (HyIS) from 2021 to 2022. From 2023 onwards, the HyIS forum will expand and evolve into the ‘Breakthrough Technology Conference,’ overseen by the worldsteel. POSCO will continue to accelerate low-carbon technology development in the steel industry through collaboration with global steelmakers, fostering cooperation over competition.
-
2021 World’s First International Hydrogen Reduction Ironmaking Forum
-
2022 HyIS Forum
Opening of the POSCO Hydrogen Reduction Ironmaking Development Center (January 2024)
The Hydrogen Reduction Ironmaking Development Center at Pohang Steelworks is home to several key departments: the ‘HyREX Project Team’ overseeing the initiative, the ‘Investment Planning and Engineering Office’ dedicated to managing investment projects, the ‘Low Carbon Iron and Steel Making R&D Center’ leading research and development, and ‘POSCO E&C’ responsible for design. These units have consolidated their capabilities by co-locating at the center. By integrating all stages from technical research to facility construction and pilot operations, POSCO aims to establish a demonstration plant that will lay the foundation for the realization of its proprietary hydrogen reduction ironmaking technology, HyREX.
-
Opening Ceremony of the Hydrogen Reduction Ironmaking Development Center
-
Panorama of the Hydrogen Reduction Ironmaking Development Center