Safety
Organization
POSCO’s Safety & Health Planning Office serves as the central control tower for company-wide safety and health management. At both the Pohang and Gwangyang Works, a dedicated Disaster Prevention Group is established to oversee site-specific safety operations. Each steelwork is staffed with professional safety management personnel, in addition to on-site safety supervisors and part managers. To further enhance safety oversight, Life Keepers1) are deployed to monitor and manage high-risk tasks separately.
1)Life Keepers are support personnel assigned to six types of high-risk tasks—such as entrapment and falls—to ensure the implementation of safety measures and guide workers away from unsafe behaviors.
Safety Advisory Committee
Since May 2022, POSCO has operated the Safety Advisory Committee, which consists of the Chief Safety and Health Officer (CSO) and nine internal and external safety experts. In 2024, the committee met three times to review our safety strategies, set directions for safety training, and explore ways to promote autonomous safety management. In 2025, the committee will place greater focus on strengthening supervisory accountability and enhancing the safety performance of contractors.
Group Safety Council
Group Safety Council Operating Framework
Category | Participation | Major Activities | |
---|---|---|---|
Group Companies | Overseas Subsidiaries | ||
Steel Sector Sustainability Council | CEO | Representative President | Share and respond to ESG issues in the domestic and global steel industry |
Group Safety Council | Safety Executive | Safety Executive | Share the POSCO Group’s safety and health performance and review relevant monitoring systems |
POSCO Safety Council | Safety Executive | - | Share POSCO’s Safety and Health Achievements |
Meeting History and Key Agenda Items of the Group Safety Council
Date | Key Agenda Items |
---|---|
Mar. 26, 2024 | · Current Status and Plans for Supporting Safety Systems at Contractors with Fewer than 50 Employees · Plans for Safety Education and Training Focused on Practical Exercises, Hands-On Experiences, and Group Discussions · Current Status of POSCO’s Mental Care Initiatives |
Oct. 23, 2024 | · Enhancing Safety Management for High-Risk Operations Under the Leadership of Plant Managers · Progress of POSCO Safety and Health Platform Expansion to Group Companies · Outcomes of Practical, Task-Specific Training Programs and Safety Operation Competitions |
Operational Status
10 Must-follow Safety Rules
Since 2004, POSCO has implemented the “10 MUST-FOLLOW SAFETY RULES” In July 2023, POSCO announced a revised version of these rules, reflecting changes in the work environment and feedback from stakeholders, including employees. The revised “10 Major Safety Rules” are applied to both domestic and overseas workplaces, and have also been shared with group companies to serve as a reference for establishing safety rules suitable for each company.
Nine Elements of the OH&S Management
To ensure systematic compliance with the Serious Accidents Punishment Act and build a world-class safety system, we have established and implemented nine core elements within our Occupational Health and Safety (OH&S) Management System.
1. Management Commitment and Goals
POSCO has appointed a Chief Safety and Health Officer (CSO) to ensure accountable and strategic oversight of all safety and health matters. Also, POSCO has established OH&S Management Policy to clearly affirm that safety takes precedence over all other priorities—including production, quality, construction schedules, and delivery deadlines.
2. Organization, Staff, and Budget
POSCO’s Safety & Health Planning Office, operating under the direct supervision of the CEO, serves as the company-wide control tower for safety, enabling responsible management and swift decision-making. Through close communication with each business site, the office promptly identifies safety issues and formulates effective response measures. It also contributes to enhancing overall safety standards by monitoring safety activities and sharing best practices to support the achievement of company-wide safety goals.
3. Two-Way Communication
We have established a variety of safety communication channels for employees, directly managed companies, and contractors. Through these channels, company representatives—including the heads of steelworks and plant managers—actively listen to the voices of both POSCO employees and contractor workers to help shape our safety and health goals and policies.
Category | Participants | Frequency | Key Activities |
---|---|---|---|
POSCO Safety Council |
Head of the Safety & Health Planning Office·Executives of the Pohang and Gwangyang Works, Representative of the POSCO Representative Body·Representative of Contractors |
Semi-annually | Share POSCO’s Safety and Health Achievements and Review the Management System |
Group Safety Council |
Safety Executives of Group Companies and Overseas Subsidiaries | Semi-annually | Share POSCO Group’s Safety and Health Achievements and Review the Management System |
Industrial Safety and Health Committee | Head of Works (Chair), Representatives of Labor (including the POSCO Representative Body), Representatives of the Company | Quarterly | Deliberate on and resolve major on-site safety and health issues (including the establishing of accident prevention plans and employee safety and health training) |
Business Unit | Deputy Head of Works·Head of Departments (Presiding at each sector level), Representative Directors of Contractors | Monthly | Share Analysis of Safety and Health Performance and Improve Activities by Plant |
Labor-Management | Plant Managers of Each Plant (Presiding), Safety Personnel of Contractors, Labor Representative Employees | Weekly | Share Safety and Health Issues by Plant and Listen to VOE (Voice of Employee) |
4. Hazardous Risk Factors Management
- Analyze and identify frequently occurring safety incidents at the plant level
- Conduct company-wide analysis of high-risk and hazardous conditions, and provide monthly feedback
- Hold hazardous risk management performance review meetings: semi-annually at the company level, quarterly at the site level, and monthly at the plant level
Category | User Target | Number of Findings | Major Improvements | |
---|---|---|---|---|
2023 | 2024 | |||
Safety Reporting System | All personnel entering steel works | 1,024 | 1,125 | Improve unsafe conditions related to safety installations and equipment around worksite, unsafe work practices, and hazardous risk factors, with a focus on high-risk categories |
Hazardous Risks Identification | POSCO employees and contractor workers | 41,564 | 39,556* |
5. Contractor Management
We operate the Safety shared growth Certification System to pre-assess safety compliance among external contractors, provide support for addressing any deficiencies, and grant workplace access only to those who meet our standards. In addition, through the “Mobile Safety Bus” program, we provide safety training and personal protective equipment (PPE) wearing practice for affiliates with insufficient safety training conditions.These buses also serve as on-site heat shelters. In 2024 alone, a total of four buses provided training to more than 13,000 personnel.
6. Compliance with Laws, Regulations, and Standard Procedures
We conduct semi-annual compliance checks on the fulfillment of obligations under the Serious Accidents Punishment Act at our worksites, continuously identifying and addressing areas for improvement. In addition, at Pohang and Gwangyang Works, the safety management departments take the lead in fostering a safety-oriented culture that strictly adheres to basic safety guidelines and standards by conducting continuous and thematic safety audits and diagnostics.
In 2024, we identified approximately 3,430 non-conformities across our steelworks through ongoing safety patrols and implemented corrective actions. An additional 200 issues were identified and resolved through safety diagnostics conducted prior to the restart of long-term maintenance sites. We also conducted special inspections of entrusted facilities and electrical rooms, as well as assessments of safety management processes for maintenance investment projects, to ensure full compliance with legal and institutional requirements and to continuously enhance overall safety management standards across the steelworks.
7. Accident Investigation and Management
In the event of an accident, POSCO informs all employees of the relevant facts, investigates the case, and develop and implement measures to prevent recurrence. We have a dedicated helicopter and a system linked with medical institutions for the transport and treatment of emergency patients. More specifically, in emergencies, response actions are taken in accordance with the Rapid Response Guidelines for Serious Accidents, available via the top navigation menu under SAFETY > RISK MANAGEMENT.
8. Education and Training
POSCO provides a safety education program that emphasizes hands-on training, interactive discussion, and practical application. We also support the enhancement of safety training systems at our partner companies. To further strengthen our capabilities in process safety management, we are reinforcing our Process Safety Management (PSM) system through the Plan–Do–Check–Action (PDCA) cycle. This includes hiring external PSM experts and cultivating internal instructors—355 of whom had been trained as of 2024. Additional efforts to prevent serious industrial accidents include upgrading the development and management of Piping and Instrumentation Diagrams (P&IDs) at our steelworks and implementing an Isolation and Locking System (ILS) based on P&IDs.
Pre-Entry Training for Worksite Access
We operate a pre-entry training system that grants worksite access only to individuals who have completed the required training. This ensures a thorough understanding of key safety protocols and potential work-related hazards. Workers are encouraged to proactively identify risks and establish appropriate countermeasures to prevent injuries. Key safety procedures include compliance with the ILS, obtaining a Safe Work Permit, participating in Toolbox Meetings (TBMs), and assigning Life Keepers to monitor site safety.
9. Evaluation and Improvement
POSCO holds monthly management briefings to assess whether the goals set under our OH&S Management Policy are being achieved as planned. These meetings also review and analyze the causes of accidents, major near-miss incidents, and occupational injuries, along with the effectiveness of subsequent safety and health initiatives. The Pohang and Gwangyang Works undergo regular external safety inspections as part of our ISO 45001 (Occupational Health and Safety Management Systems) certification. In 2024, we implemented improvement measures based on inspection findings, addressing key issues such as port safety management and access control to electrical rooms. These actions have been integrated into our company-wide risk management framework.
SmartSafe Tech
POSCO deploys AI, IoT, and other smart technologies to reduce safety blind spots at worksites and secure the safety of workers. Through the introduction of smart safety inspection and monitoring technologies, we proactively identify hazardous risk factors and replace human workers with robots in high-risk tasks—aiming to eliminate the potential for serious workplace accidents.
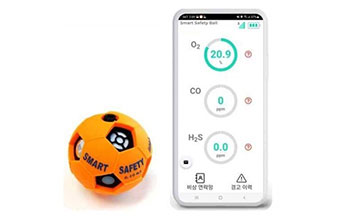
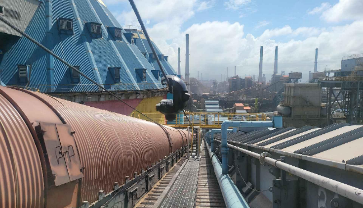
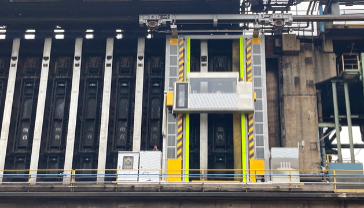
POSCO continues to develop and implement various safety solutions incorporating smart technologies. In 2024, we deployed a quadruped robot to the blast hole of a furnace at Gwangyang Works. The blast hole is a critical piece of equipment that requires constant monitoring due to the potential risk of gas leaks. The remotely operated autonomous quadruped robot conducts real-time inspections along pre-programmed routes and enables operators to monitor conditions without the need for direct access to the furnace. Additionally, it enhances safety through continuous monitoring by analyzing inspection data in real time and issuing alerts when abnormalities are detected.
Meanwhile, a wheeled robot was developed and deployed in the underground electrical room of the Gwangyang No. 4 Hot-Rolling Mill to conduct unmanned equipment inspections. Due to the presence of high-voltage currents, operators in electrical rooms are constantly exposed to the risks of electric shock and explosion. In 2024, we developed and deployed an autonomous wheeled robot at the site, as it is better suited than a quadruped robot for areas with sloped access roads. The robot enables real-time monitoring and data analysis without requiring workers to be physically present. To further reduce the operational burden on operators, an on-site charging station was also installed. Looking ahead, we will continue to develop and implement smart technologies to create a safer work environment.
-
Quadrupedal inspection robot for unmanned facility monitoring
-
Autonomous wheeled robot
Risk Management
Emergency Response Plan
Emergency Response Procedures
POSCO operates the Serious Accident Rapid Response Guidelines to ensure swift and structured action in the event of an emergency. These guidelines outline clear emergency response procedures, including the formation and operation of a Rapid Response Taskforce led by the CSO, who reports directly to the CEO during such events. To further strengthen emergency preparedness, we maintain an emergency medical transportation system utilizing our company helicopter and partner with medical institutions to ensure patients receive timely and optimal care.
Goals
POSCO Safety Management Goals
POSCO operates both the Total Recordable Injury Frequency Rate (TRIFR) and the existing Lost Time Injury Frequency Rate (LTIFR) to enhance employee awareness of safety and health. This dual-metric approach fosters a culture of transparent reporting—even for minor incidents—and reinforces preventive safety management practices. We incorporate quantitative safety indicators into the KPIs and apply safety incentives to non-executive employees. This framework sets clear targets and performance standards, directly linking safety outcomes to compensation policies and encouraging both executives and employees to achieve measurable results.
Category | 2024 Performance | 2025 Goals | |||
---|---|---|---|---|---|
LTIFR | 0.83 | 0.60 | |||
TRIFR | 1.81 | 2.12 | |||
Number of Serious Accident Victims | 0 | 0 |
Safety KPIs for Executives
- 25% of the CEO’s KPI is tied to the number of serious accident victims at domestic worksites.
- 25% of each head of steelworks’ KPI is tied to the number of serious accident victims at their respective steelworks.
Employee Safety Awards Program
POSCO operates various programs to recognize outstanding safety practices across the organization. In 2024, a total of 176 awards were presented, including the Safety Grand Award, Accident-Free Plant Award, Excellent Safety Organization Award, and Individual Safety Award.
Safety Performance
Performance and Goals
2024 Achievements | 2025 Action Plans |
---|---|
• Promoted innovative implementation of safety management systems, standards, and procedures • Strengthened safety management practices focused on execution to prevent serious accidents • Conducted thematic inspections of vulnerable areas, reestablished process safety management systems, and enhanced safety training programs |
• Reinforce practical actions focused on the essence of accident prevention and establish a self-directed safety management system. • Improve the effectiveness of on-site safety management systems and build an autonomous and accountable implementation framework • Enhance employee acceptance and internalization of safety practices through the practical and efficient operation of safety systems. |
Key Safety Improvement Performance
Course Name | Number of Participants |
Target Classification | ||||
---|---|---|---|---|---|---|
Directly | Group | Partner | Service | Subcontractors | ||
Executive Safety Leadership Program | 165 | ● |
|
|
|
|
Safety Leadership Program for Employees (by Stage in Career Cycle) | 1,481 | ● |
|
|
|
|
PSM Professional Training Program | 2,032 | ● |
|
|
|
|
Safety Competence Training for Contractors (by Tier) | 18,785 |
| ● | ● | ● | ● |
On-Site Safety Bus Program | 13,182 | ● | ● | ● | ● | ● |
Pre-Entry Training for Worksite Access | 66,246 |
|
|
| ● | ● |
POSCO’s Four Major Emergency Drills
Category | Safety and Disaster Prevention Group | Environment and |
||||||||||
---|---|---|---|---|---|---|---|---|---|---|---|---|
Firefighting (Annually) |
PSM | Confined Space | Chemical Spills |
|||||||||
Target | Performance | Rate | Target | Performance | Rate | Target | Performance | Rate | Target | Performance | Rate |
|
Pohang Works | 68 | 68 | 100% | 78 | 78 | 100% | 127 | 127 | 100% | 32 | 32 | 100% |
Gwangyang Works | 69 | 69 | 100% | 65 | 65 | 100% | 122 | 122 | 100% | 46 | 46 | 100% |
R&D Center | 6 | 6 | 100% | (N/A) | - | - | 4 | 4 | 100% | 1 | 1 | 100% |
Administration Support Group | 3 | 3 | 100% | (N/A) | - | - | 3 | 3 | 100% | (N/A) | - | - |