Decarbonization Roadmap
Roadmap
In 2024, POSCO set a carbon emissions target of 75.7 million tons, with actual performance recorded at 71.1 million tons.
1)The above information is subject to change depending on internal and external circumstances.
2)The baseline figure refers to the average total emissions from POSCO’s domestic operations over the period 2017-2019.
Climate Change Management
POSCO incorporates climate change response into all levels of its decision-making system. Climate-related strategies and facility investment plans are reviewed and deliberated by the ESG Committee, which operates under the Board of Directors. The Carbon Neutral Committee, chaired by the CEO, oversees departmental implementation of carbon neutrality and coordinates any issues that arise during execution. It serves as the control tower for climate action. At monthly management meetings, greenhouse gas emissions performance is tracked alongside the financial impacts of climate response initiatives.
The Technology Strategy Office, which reports directly to the CEO, serves as the secretariat for the six subcommittees of the Carbon Neutrality Committee, which are responsible for establishing decarbonization strategies, developing related technologies, and monitoring implementation at the Pohang and Gwangyang Works. To support a smooth transition to a carbon reduced steel production system, we are strengthening our execution capabilities through two dedicated teams: the HyREX Project Team, which oversees the hydrogen reduction ironmaking project under the direct supervision of the CEO, and the Electric Arc Furnace Project Team, which is based at Gwangyang Works.
Blast Furnace-Based Technologies
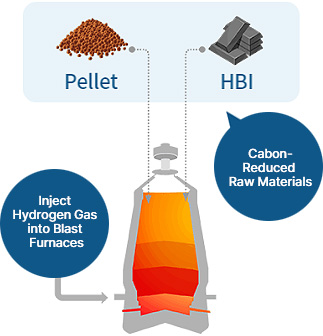
Application of Carbon-Reduced Raw Materials
Iron ore used in blast furnaces can be broadly categorized into sinter and pellets, with sinter accounting for more than 70%. Pellets are raw materials formed into uniform spherical shapes after crushing and sorting iron ore.
Simply replacing sinter with pellets in blast furnace operations can reduce fossil fuel use in the sintering process. Hot Briquetted Iron (HBI) is a pre-reduced form of iron ore from which oxygen has been removed. When used in a blast furnace, HBI reduces the amount of metallurgical coal required for the reduction process. We are advancing HBI production projects in Australia and the Middle East to ensure timely access to HBI for use in the production of our carbon-reduced steel products.
Application of Hydrogen-Containing Gas
Carbon emissions can be significantly reduced by using natural gas (NG), a carbon-reduced fuel, in place of metallurgical coal. When reformed, methane (CH₄), the primary component of NG, breaks down into carbon monoxide (CO) and hydrogen (H₂). The resulting hydrogen-containing gas can be injected into the blast hole at the bottom of the furnace as a reducing agent, thereby lowering the amount of metallurgical coal needed in the reduction process.
In the first half of 2023, POSCO completed a new NG injection facility to establish this technology, and is now working to develop hydrogen injection capabilities. We plan to package this blast furnace-based bridge technology, with the ultimate goal of establishing a carbon reduction steelmaking model based on blast furnace operations.
Converter-Based Technologies
A converter is a large cauldron-like facility that holds molten iron produced in a blast furnace. Oxygen is blown into the molten iron to remove impurities and adjust the composition of molten steel as needed. We estimate that approximately 80% of the total carbon emissions associated with producing one ton of molten steel are generated during the production of molten iron. Accordingly, the converter-based bridge technologies focus on reducing the volume of molten iron used while increasing the proportion of scrap charged into the converter. There are two main approaches to achieving this:
Melted Scrap Charging Method
Oxygen Top & Bottom Blown Converter
The second is the Oxygen Top & Bottom Blown (OTBB) Converter technology, which secures an additional heat source to increases the use of steel scrap in the converter by blowing oxygen from both the top and bottom. Without relying on external heat, the converter instead utilizes the heat from the molten iron itself. As more scrap is added, the temperature of the molten iron decreases. The advantage of using an OTBB Converter is that it maximizes secondary combustion and heat transfer efficiency by injecting oxygen from both the top and bottom of the converter.
-
Melted Scrap Charging Method
-
-
OTBB Converter technology
-
Technologies that enable the use of large amounts of scrap iron in place of molten iron―such as the Melted Scrap Charging Method and OTBB Converter technology―are collectively referred to as “low Hot Metal Ratio (HMR) operation technologies.”
Scrap Usage
Category | 2024 | 2030 Target |
---|---|---|
Scrap Usage | 6,879 | 9,200 |
purchased scrap | 2,052 | 5,000 |
self-sourced scrap | 4,827 | 4,200 |
EAF-Based Technology
CCUS
POSCO is exploring the application of Carbon Capture, Utilization, and Storage (CCUS)1) technology to reduce CO2 emissions generated during the steelmaking process.
1)CCUS refers to a technology that captures large volumes of CO₂ emissions and either utilizes them directly for industrial purposes, converts them into high value-added products, or stores them permanently or semi-permanently.
Carbon Capture, Utilization (CCU)
We are reviewing a project to produce liquid carbonic acid with 99.99% purity and sustainable aviation fuel (SAF) using by-product gases generated from our steelworks. Through this initiative, we aim to gradually expand our industrial gas portfolio. In 2024, we established the Steel Industry CCU Consortium in partnership with LG Chem, the Korea Research Institute of Chemical Technology (KRICT), and the Gyeongsangbuk-do Provincial Government. The consortium is currently participating in the CCU Mega Project led by the Ministry of Science and ICT (MSIT), and has proposed Pohang Works as the demonstration site. Final approval was granted by MSIT in October 2024, and the demonstration is scheduled to begin in 2026 following a preliminary feasibility review in 2025. The CCU Consortium plans to demonstrate a technology at Pohang Works that captures CO₂ from by-product gas generated during the steelmaking process and converts it into syngas―a mixture of carbon monoxide (CO) and hydrogen (H₂). This syngas can either be sold externally as a raw material for chemical products such as sustainable aviation fuel (SAF), or injected back into the steelmaking process to serve as a reducing agent for iron ore, thereby creating an efficient resource circulation system.
Carbon Capture, Storage (CCS)
HyREX
Hydrogen reduction ironmaking is a technology that reduces greenhouse gas (GHG) emissions by replacing metallurgical coal―traditionally used as a reducing agent and heat source in the steelmaking process―with hydrogen. In 2024, our HyREX technology was designated as a National Strategic Technology in recognition of its critical importance to national security and its broad economic impact. That same year, the Ministry of Science and ICT (MSIT) selected the Optimized Iron Ore Technology Development for Korean Hydrogen Reduction Ironmaking (Steel) project as a Global R&D Flagship Project. In line with national policy projects, we are currently preparing the Korean-type Hydrogen Reduction Ironmaking Demonstration Project, aiming to complete technological development by 2030.
HyREX Features
HyREX Deployment Status and Future Plans
In 2021, POSCO began the site permitting and approval process for the construction of a hydrogen reduction ironmaking plant at Pohang Works, covering an area of 1.35 million ㎡ (approximately 410,000 pyeong). The following year, in July 2022, we signed an engineering partnership agreement with Primetals Technologies, a company with extensive experience in designing FINEX facilities. Through this partnership, we are jointly designing the key facilities for the HyREX demonstration plant, with the aim of constructing a 300,000-ton-per-year test facility at Pohang Works.
Building on these efforts, in 2023, POSCO introduced a hydrogen fluidized bed reduction experimental furnace with a capacity of 50 kg per batch at RIST to validate the hydrogen-based reduction technology. This was followed in April 2024 by the completion and successful first test of a 1-ton-per-hour electric smelting furnace (ESF) experimental facility at Pohang Works. These milestones have laid a solid foundation for the development of core element technologies for both the fluidized bed reduction furnace and the ESF and the HyREX process.
In January 2024, we established the HyREX Project Team to lead the development of hydrogen reduction ironmaking technology and launched the Hydrogen Reduction Development Center to bring together experts from across our group companies. Looking ahead, we aim to construct a demonstration plant that will serve as a cornerstone for the implementation and future commercialization of HyREX technology.
At the global level, POSCO is also actively building international technology partnerships to advance decarbonization in the steel industry. In 2021 and 2022, in collaboration with the World Steel Association (worldsteel) and Swedish steelmaker SSAB, we led efforts to launch the Hydrogen Iron & Steel Making Forum (HyIS Forum), which in 2023 was expanded into the Breakthrough Technology Conference organized by worldsteel. Since 2023, POSCO has taken a leading role in organizing and operating the HyREX R&D Partnership as a dedicated platform for building global consensus on HyREX technology. The partnership, comprising 19 related companies―including global steelmakers, raw material suppliers, and energy firms―held its first HyREX R&D Partnership Conference in November 2024. Through this initiative, we aim to accelerate the development of carbon reduction technologies for the steel industry in close cooperation with global partners.
In July 2024, POSCO and Primetals Technologies signed a Memorandum of Understanding (MOU) to jointly design and construct a HyREX demonstration plant. Primetals Technologies brings expertise in FINEX design technology.
Building on this agreement, POSCO will concentrate its efforts on developing a demonstration plant to validate the commercial viability of hydrogen reduction ironmaking by 2030, while also preparing to meet decarbonization targets through an economically viable hydrogen infrastructure.
-
2021 World’s First International Hydrogen Reduction Ironmaking Forum
-
2022 HyIS Forum
-
HyREX Development Center (2024)
-
2024 HyREX R&D Partnership Conference
Decarbonization Deployment
Green Partnership
Since 2003, POSCO has participated in the Carbon Disclosure Project (CDP) to ensure the transparent disclosure of climate-related information. In 2020, we became the first Korean manufacturer to declare support for the Task Force on Climate-related Financial Disclosures (TCFD) and began disclosing carbon data in line with its recommendations. In 2024, POSCO was rated B for Climate Change and received an A- in the CDP Water Security evaluation.
Scope 3 Management
Since 2022, POSCO has conducted third-party verification of its Scope 3 emissions in accordance with ISO 14064-31) standard, as disclosed in our Annual Sustainability Report. Building on these efforts, in 2024, we established a working group comprising POSCO and POSCO FLOW―our group’s logistics company―to enhance the calculation methodology for purchased raw materials and related transportation.
1)ISO 14064-3 is a standard that provides guidelines for the validation and verification of greenhouse gas (GHG) statements.
Internal Carbon Pricing Initiative
Carbon-Reduced Steel
POSCO is advancing the development of carbon-reduced steel to meet our customers’ decarbonization demands.
We aim to reduce carbon emissions per ton of crude steel by approximately 10%1) compared to existing blast furnaces, by adopting a dual scrap charging technology that increases the scrap ratio during the steelmaking process. In addition, we are accelerating our efforts to achieve continuous carbon reduction by constructing a new large electric arc furnace (EAF), which can reduce carbon emissions by up to 75%2) compared to existing blast furnaces.
1)The target figure is based on the carbon emission intensity defined in POSCO’s Environmental Product Declaration, certified by the MOE in 2021.
2)The target figure is based on the 2017-2019 average, POSCO’s baseline period for carbon reduction.
POSCO's Carbon-Reduced Steel Product Lineup
Core Technology | Carbon Reduction Target | Production Process |
---|---|---|
Two-Batch Scrap Charging | ↓10% | Increase the scrap usage by charging scrap twice in the steelmaking process |
Large EAF | ↓75% | Produce steel using scrap in a newly constructed large-scale EAF |
Recycled Material Purchasing
POSCO comprehensively manages its annual scrap procurements.
In 2024, the total volume of ferrous scrap imported or purchased domestically amounted to 1,924 thousand tons, with an associated cost of KRW 929.6 billion. Additionally, recycled material purchases ―such as increased recycling of used and waste materials―totaled KRW 315.7 billion in the same year.
Steel Scrap Procurement: Domestic and Imported
Year | Quantity | Amount |
---|---|---|
2023 | 218.0 | 1,198.1 |
2024 | 192.4 | 929.6 |
3R Practices in Equipment and Materials Procurement
Category | Project Name | 2023 |
2024 |
Calculation |
---|---|---|---|---|
Reuse | Expansion of Used Material Recycling |
52.6 |
59.3 |
• Unit cost or proportion of new materials used in place of used materials Σ {Usage × Unit cost of new materials × 60% (Class A) or 15% (Class B)} |
Expansion of Repaired Recycling Materials | 120.4 |
111.5 |
• Amount of recycled material received (with QS code) after repair |
|
Reduce | Expansion of Eco-Friendly Refractory Materials | 129.2 |
132.0 |
• Amount of eco refractory materials received, containing at least 5% recycled content from waste refractory materials |
Recycle |
Use Copper Recovery from Waste Cables |
5.7 |
12.9 |
• Copper recovered from waste cables + copper scrap in waste air vents * Σ (Recovered copper from waste cables, etc. × Purchase price of copper) |
Total |
307.9 |
315.7 |
- |